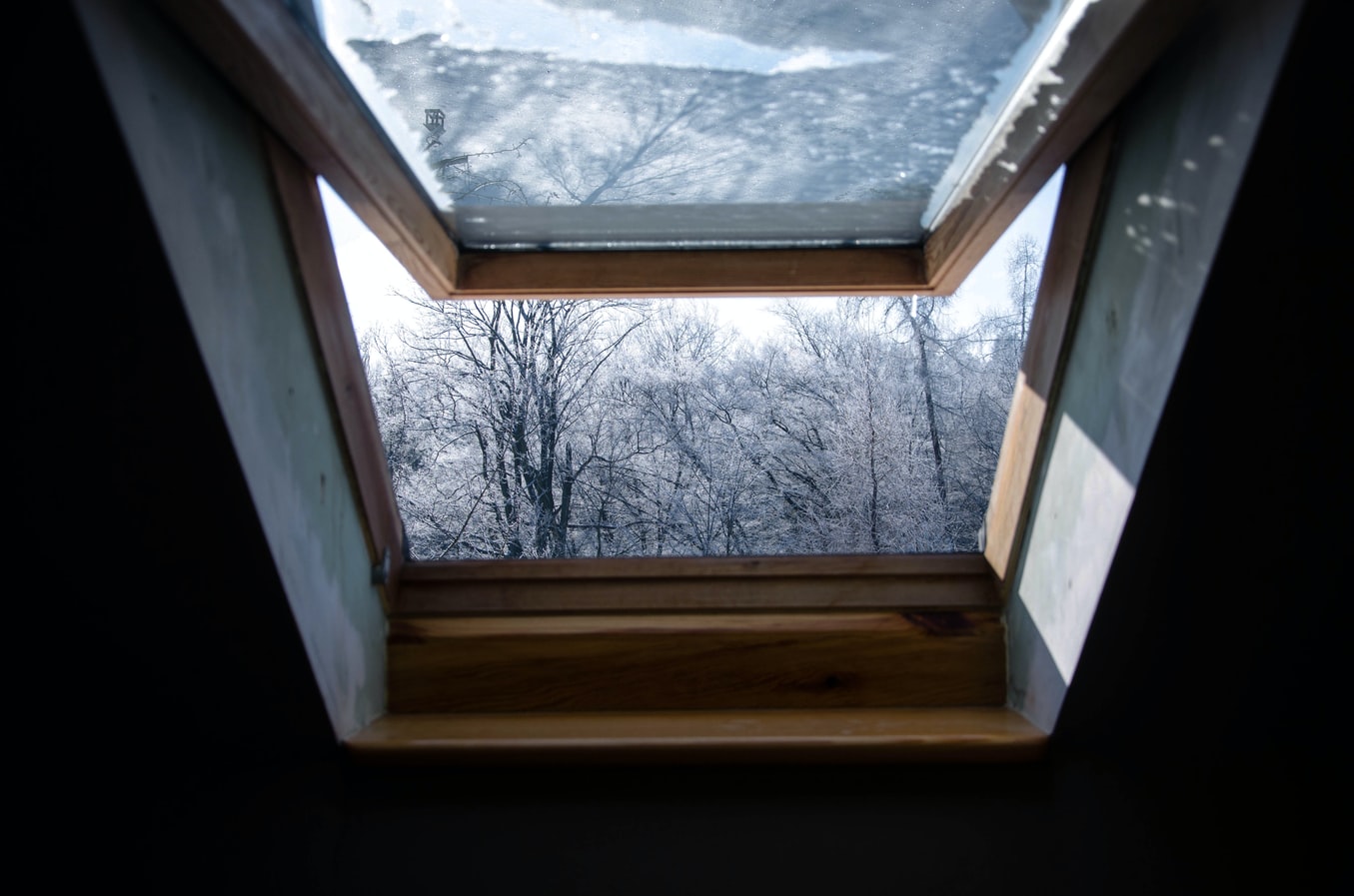
One of our clients approached us with a request to add skylights to a a new warehouse building project that was under design. They saw several benefits: the natural light would decrease the need for artificial light and the cost payback should be great. Furthermore, their workers would benefit from having natural light. It would be another sustainable feature for the facility.
As gratifying as it is to have a client who wants to create as green a facility as possible; with a positive return on the additional investment. Occasionally, we need to limit the enthusiasm when the sustainable solution is actually less sustainable than a conventional design:
-
Not the best return: If the most cost-effective solution to warehouse lighting is a project goal, then high bay fluorescent lights and occupancy/vacancy sensors offer a far better return than relying on passive lighting from skylights. A single 4-lamp T5HO fixture running for 8 hours a day, 20 days a month costs roughly $3.50 monthly. The local climate calculations will suggest the actual number of hours each year that are sunny enough to allow artificial lighting to be turned off. If one skylight replaces one light fixture, for an average of 20 hours per week, that’s only $21 in savings per year.
-
Total construction costs: The costs of a skylight will depend on whether it will be part of new construction (less expensive) or cut into existing construction (more expense). There is additional cost for rewiring light fixtures to automatically turn off or dim. Should the skylight be strong enough to support a person falling onto it, or are guard rails around the skylight a better option? Both options add more cost. And sometimes a screen is needed below the skylight to catch any debris that might occur from a shattering of the skylight.
-
Life cycle costs: Any calculations on cost savings due to skylights must include life cycle costs. The flashing around a skylight is a maintenance concern and possible operational risk if a leak occurs. As designers, we do all that we can to minimize the number of roof penetrations. When natural light is mandated, we often propose clerestory windows or light wells, employing the same principle as the iconic sawtooth roofs of a century ago. However, if the roof must have smoke vents, these are available as skylights. Even the maintenance costs associated with cleaning bird droppings need to be incorporated into the thought process.
-
Effectiveness: Given land cost premiums, warehouses today are being designed ever taller, approaching the 45’ maximum height in which an ESFR sprinkler system can be deployed. The result is tall pallet racking that creates the visual effect of canyons. Although skylights can be centered on forklift aisles, how much natural light actually reaches the floor to provide adequate lighting to read markings or reach exits?
-
Actual time in warehouse: One key to effective warehouse operation is to minimize the manhours needed for operations. Short of full automation (AS/AR), the goal is typically to spend as little time in the warehouse as possible; complex algorithms are developed with the intent of reducing time in stacking and retrieving. Thus, the actual time people might benefit from being in natural light is to be minimized, decreasing any indirect benefits of skylighting.
PRODUCTION SPACES
Do some of the same arguments apply to production areas? These areas typically have lower ceilings and are continually occupied. And yet, they can be plagued with additional unintended consequences resulting from skylights.
An example comes from a Maryland-based electronics manufacturing client. Our first tour of their plant revealed the aesthetic of tarps hung below the skylights, over the work benches from October to March each year. Our first thought was potential leakage from the skylight at its flashing to the roof, but there was no evidence of that from our inspection. We then concluded that conditioned/humidified air from inside the building was condensing on portions of the skylight installation. But how could that be?
The skylight vendor identified the insulation value of the skylight assembly as R=2.0. This is equivalent to a triple glazed window assembly. However, this is the average value; there were portions of the assembly where there was little or no thermal break. This design, coupled with the need to keep the plant at a relative humidity of about 40%, was calculated to determine that condensation would begin to occur at an exterior temperature of about +44oF. Such lower temperatures typically occur at least part of day in this region between October and March. Whereas interior condensation on a window may collect on the window sill, on a skylight it becomes dripping water. Some designs offer a way of collecting condensation in expectation that it will evaporate over time; other times the condensation exceeds the holding capacity. In the case of this facility, the condensation often froze at night, and then melted as the daytime became warmer. Janitors emptied the tarps of water each evening.
Another example is a Midwest bakery with skylights that experienced dripping only in the washdown area. For the same reasons stated previously, the humidity in that area resulted in an unacceptable amount of dripping from the skylights.
Ultimately, even minimal humidity, coupled with the coldest night conditions, will result in condensation in any building in almost any climate. The question becomes what amount of condensation, if any, is acceptable. In an electronics plant, some dripping a few days per year may be acceptable. In a food processing plant, condensation may be an opportunity for bacteria growth and insect infestation, no matter how well that condensation is contained within the skylight assembly, which offers another reason why skylights may not be an appropriate option.
The electronics manufacturer is now testing our proposed fix, which will reduce the dripping to +3oF exterior conditions. As for the bakery, they removed the skylights from the washdown area.
◗ Want to know more about how NUTEC can work with you to address your skylight needs? Contact Dominic Lizzi at 717.434.1553 or email him at dlizzi@teamnutec.com.